
A significant advancement in lithium extraction has emerged from recent research, which has the potential to further the global energy landscape.
The Korea Institute of Fusion Energy (KFE) unveiled its latest breakthrough by showcasing a study that achieved a threefold increase in lithium extraction efficiency compared to conventional methods.
Spearheaded by its team of researchers, the feat was achieved through the innovative application of carbon dioxide microwave plasma technology. According to the team, the implications of this development are profound, promising to address critical challenges in lithium supply for burgeoning industries such as electric vehicles and renewable energy storage.
As the demand for lithium continues to surge, fueled by the accelerating transition towards sustainable energy solutions, this novel approach holds great promise in meeting the evolving needs of a greener future, according to the KFE team.
The details of the team's research were published in the journal Desalination.
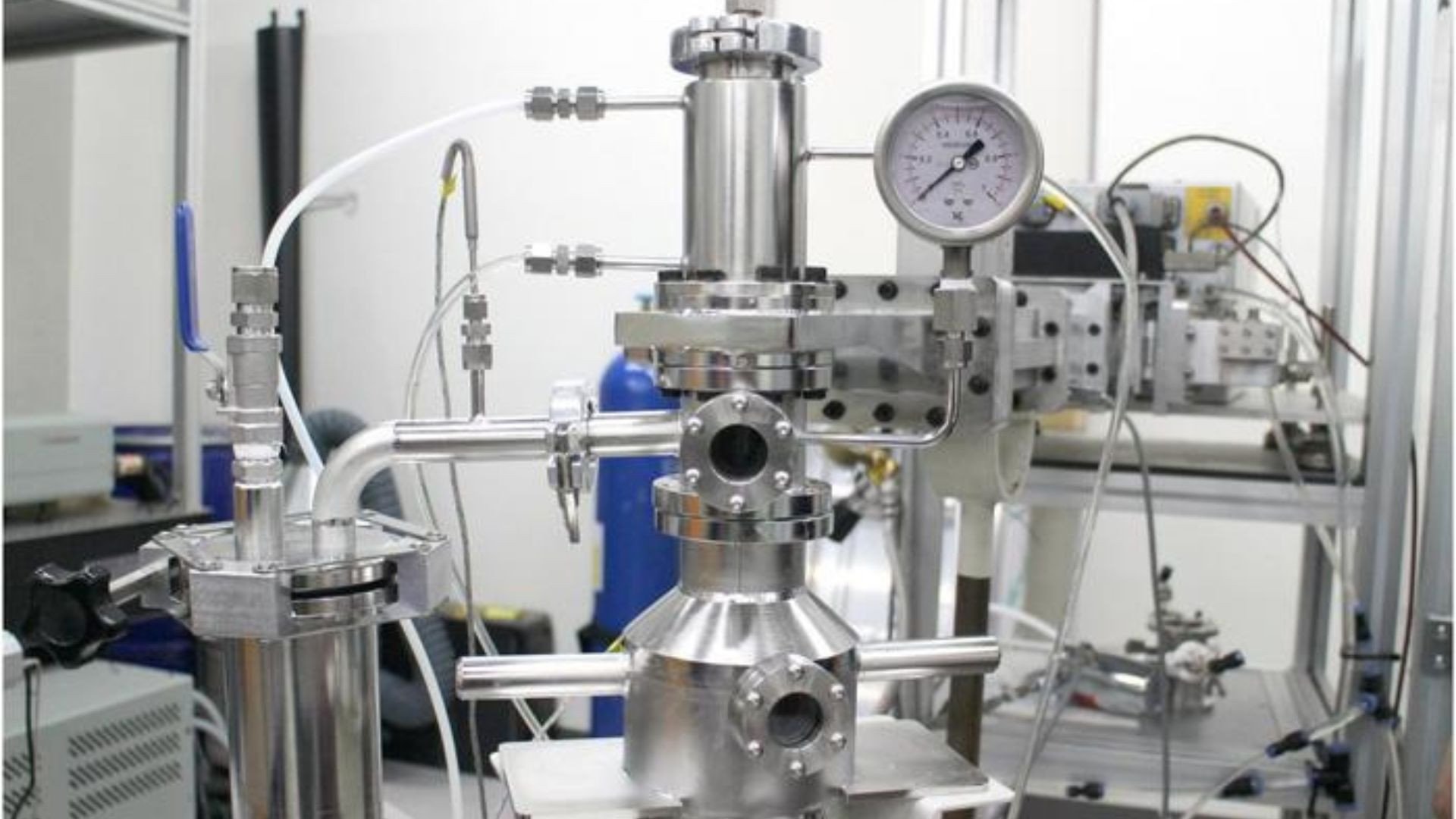
Persisting challenges
In the quest for efficient lithium extraction, two primary methods have long dominated the landscape, each with its challenges. The conventional approach involves mixing sodium carbonate (Na2CO3) with lithium-rich saltwater, yielding lithium carbonate (Li2CO3) through a complex process. However, a notable drawback emerges as the lithium carbonate becomes entangled with sodium impurities, necessitating further separation steps.
An alternative method, employing carbon dioxide gas instead of sodium carbonate, offers a potential solution. Yet, this method encounters its hurdle: low extraction rates in brine, where lithium salt forms a bond with chlorine. This presents a significant barrier, demanding further research to overcome.
Efforts to refine lithium extraction processes are underway, driven by the urgent need to meet escalating demands from industries such as electric vehicles and renewable energy storage. As scientists delve deeper into these challenges, breakthroughs hold the key to unlocking a more sustainable future powered by lithium-ion technology, according to researchers at KFE.
Promising results
The team harnessed the power of carbon dioxide microwave plasma technology to enhance lithium extraction rates significantly. This approach involves ionizing carbon dioxide into a plasma state, marking a pivotal advancement in the quest for more efficient extraction methods.
Researchers at KFE embarked on a series of experiments to compare the efficacy of carbon dioxide plasma lithium extraction with traditional methods. Utilizing simulated brine as their testing ground, their findings unveiled a staggering threefold increase in extraction rates when employing plasma technology.
According to the team, the results are highly encouraging as direct injections of carbon dioxide gas yielded a modest 10.3 percent extraction rate, and the introduction of carbon dioxide plasma propelled the extraction rate to an impressive 27.87 percent. This marks a paradigm shift in lithium extraction methodologies, offering a glimpse into the vast potential of plasma technology in optimizing resource utilization.
The KFE team claims that the research represents a watershed moment in the field, demonstrating the tangible benefits of integrating plasma technology into the lithium extraction process for the first time. "It was possible to confirm the effects of the heat and ions, electrons, radicals, etc that are generated when carbon dioxide plasma forms on lithium extraction rates," said Dr. Jong Keun Yang of KFE and the first author of the research paper, in a statement.
Researchers hope plasma-based lithium extraction processes offer a fresh avenue for advancing technology capable of efficiently extracting lithium from seawater, even in lower lithium concentrations. "Lithium obtained from seawater is a crucial component of fusion energy generation, and we will continue to conduct research into both fusion energy development and fusion energy fuel acquisition, said Suk Jae Yoo, president of KFE, in a statement.
Originally published on Interesting Engineering : Original article